China cellulose ether manufacturer
China HPMC factory,have a daily output 150 tons,our products including Hydroxypropyl Methyl Cellulose (HPMC), Redispersible Polymer Powder (RDP) ,which can be widely used in building materials such as dry mix mortar, gypsum based plaster, wall putty, tile adhesive, cement mortar, EIFS, detergent and so on.
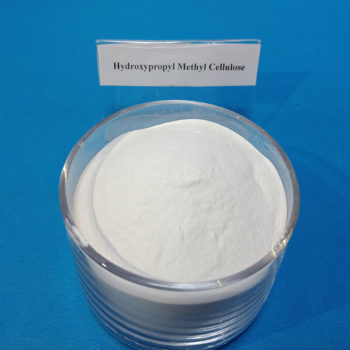
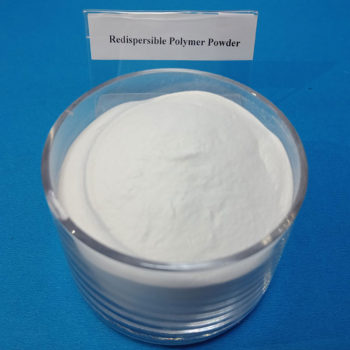
How to improve the anti-slip performance of ceramic tile adhesive
When it comes to tile installations, ensuring a secure and slip-resistant surface is crucial for safety. This article explores the vital role of Hydroxypropyl Methylcellulose (HPMC) in enhancing the anti-slip performance of ceramic tile adhesive, providing valuable insights for those seeking to elevate the safety standards of their projects.
Understanding Anti-Slip Performance:
Anti-slip performance in ceramic tile adhesive is a critical factor in preventing accidents and ensuring the longevity of installations. Surfaces that are prone to water exposure, such as bathrooms and kitchens, demand special attention to reduce the risk of slips and falls.
The Role of HPMC in Tile Adhesive:
-
Thickening and Water Retention: HPMC acts as a crucial thickening agent in tile adhesive formulations. By controlling the consistency of the adhesive, it enhances its ability to grip the tiles during installation. Additionally, HPMC's water retention properties ensure a prolonged open time, allowing for proper tile placement and adjustment.
-
Improved Workability: HPMC contributes to the workability of tile adhesive, making it easier to spread and manipulate during installation. This is particularly important for achieving a uniform and secure bond between the tiles and the substrate.
-
Preventing Sagging: The incorporation of HPMC cellulose helps prevent the sagging of tile adhesive on vertical surfaces. This is essential for ensuring that the adhesive adequately supports the weight of the tiles during the curing process, promoting a secure and durable bond.
-
Enhanced Adhesion: HPMC enhances the adhesive properties of the tile adhesive, ensuring a strong bond between the adhesive, tile, and substrate. This not only improves the overall performance of the installation but also contributes to the anti-slip characteristics of the finished surface.
Guidelines for Improving Anti-Slip Performance:
-
Proper HPMC Dosage: Ensuring the correct dosage of HPMC in the tile adhesive is crucial. Balancing the thickening effect without compromising workability is key to achieving optimal anti-slip performance.
-
Adherence to Industry Standards: Follow manufacturer guidelines for both the ceramic tiles and the tile adhesive. This includes adhering to recommended mixing ratios, curing times, and surface preparation procedures.
-
Surface Preparation: Adequate surface preparation, including thorough cleaning and leveling, is essential to achieving a strong bond. HPMC works most effectively on properly prepared surfaces.
-
Tile Selection: Choose tiles with anti-slip properties, especially for areas prone to moisture. The combination of anti-slip tiles and HPMC-enhanced adhesive creates a synergistic effect, significantly improving overall safety.
Conclusion:
Elevating the anti-slip performance of ceramic tile adhesive involves a strategic approach, with HPMC playing a pivotal role in ensuring a secure and durable bond. By understanding the specific functions of HPMC in tile adhesive formulations and following recommended guidelines, projects can achieve not only superior anti-slip performance but also enhanced overall safety and longevity.